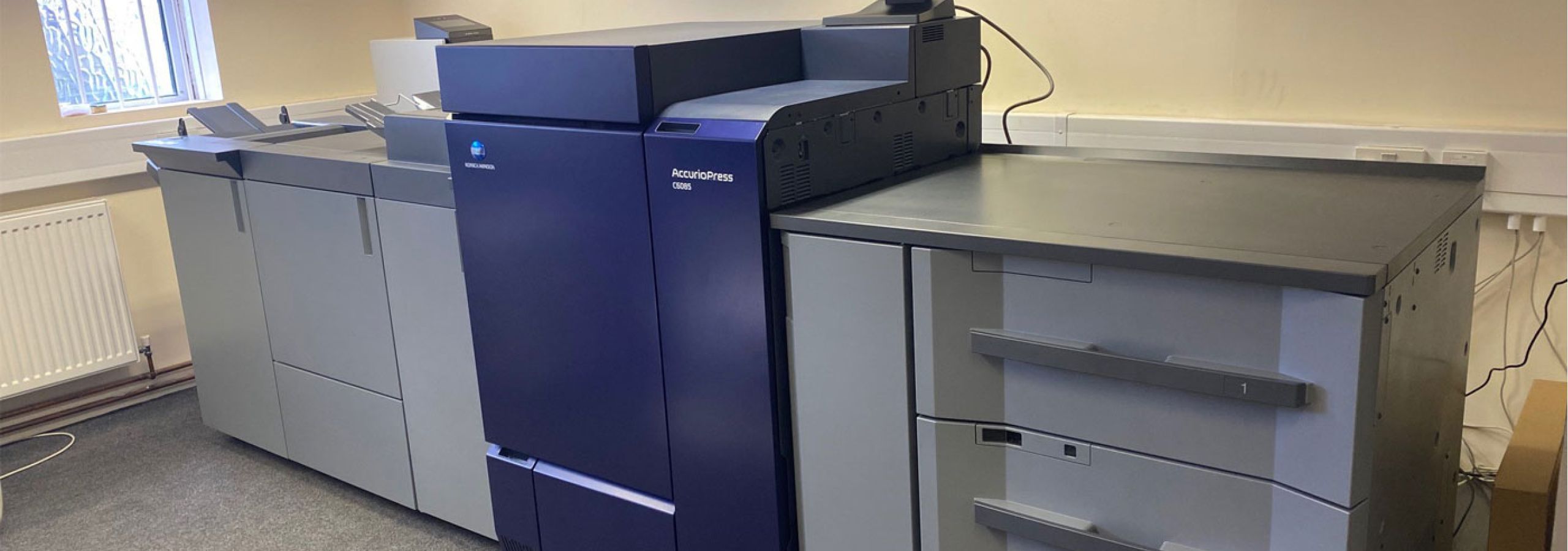
We haven’t got room for it
As their clientele expanded, the demands they placed on their equipment gradually increased. Staff began working nights and weekends, to meet deadlines. The time had come, to consider upgrading their Digital Press.
Our customer was more than aware of the opportunities available, by upgrading. Increased productivity, reduced running costs, lower staff wages, enhanced capability and quality improvements, to name a few.
They hit a major stumbling block. They did not believe that they had available space for the Digital Press that, matched their requirements. They began to contemplate relocating their premises. This would have been a costly and disruptive process, at a time when their workload was increasing. Relocation would have offset any potential cost saving incentives, for upgrading. They were facing the prospect of, becoming victims of their own success.
To glance at their Digital Print room, you would not believe that a larger, more suitable Press would fit. The layout of the room was also not optimal, from a “flow” perspective. A large table in the middle of the room contained a mixture of completed work, stock required for upcoming work and work awaiting finishing. It would quickly fill up, removing any available working space.
Armed with a camera and tape measure, we measured every dimension of the room. We went away, plotted the room, including contents in CAD software and began to re-design the room layout. We discovered that, by removing the table and re-arranging the racking, there was now an open floor.
We added two workbenches with storage underneath against the walls, where racking had been placed. Doing this doubled worktop space, whilst separating completed and incomplete work. Paper stock was moved to a rack, next to the input trays of the Press, opposed to being on the opposite side of the room.
Crucially, we discovered that the Press they required would fit, meeting all recommended space requirements. There was less than 15 centimetres extra space left!
The customer actioned our recommendations and proceeded with the upgrade. Work now flows around the room from start, to finish. They can quickly appraise stock levels and job progression.
Being able to install the best suited Press has dramatically increased Productivity. The enhanced capabilities and reduced running cost of their new Press has generated new business opportunities.
The previously installed Press was refurbished at our Workshop, ready to support it’s new owner for years to come.
If you are in a similar predicament to the customer mentioned above, or are interested in learning about second user equipment, please contact us. We look forward to hearing from you!